Aluminum Refrigerant Piping Systems
Patent No. 7079618, Patent No. 7197319,
Patent No. 7274276, Patent No. 7300313,
Unexamined Patent Publication 2022-115650
Features
- Contributing to the realization of a carbon-neutral world
Replacing copper refrigerant piping with aluminum in response to demand for copper associated with the popularization of electric vehicles is our way of contributing to the realization of a carbon-neutral world. - Streamlining refrigerant piping installation
Aluminum piping is lightweight—one-third the weight of copper piping—and does not require nitrogen replacement, reducing installation time roughly 20% compared to copper piping. - Cost advantage
Piping costs can be reduced roughly 10% compared to copper (although mechanical fittings are about the same).
Background of development
We have extensively studied aluminum refrigerant piping, which is lighter (one-third the weight), less expensive, and easier to recycle than its copper counterpart, which has long been the mainstay of refrigerant piping in construction.
In addition to working with aluminum manufacturers to establish specifications for aluminum piping, we have also teamed with Higashio Mech Co., Ltd. to develop mechanical fittings for aluminum refrigerant piping. We also jointly developed branch pipe fittings for aluminum refrigerant piping with BENKAN Corporation. Furthermore, we have made it possible to braze aluminum piping, a process long considered difficult in construction sites by selecting filler materials for aluminum, establishing brazing procedures, and providing a smartphone app* to assist with the brazing process.
- A voice guidance system that outlines the brazing process for aluminum refrigerant piping
Replacing copper refrigerant piping with aluminum
to contribute to achieving a carbon-neutral world by 2050
Our system comprises aluminum refrigerant piping (Photograph 1) and mechanical fittings (Photograph 2), branch pipe units (Photograph 3), and a brazing method for aluminum refrigerant piping (Photograph 4). We strive to streamline refrigerant piping installation and contribute to the achievement of a carbon-neutral world by further adapting the system for use in multi air conditioning systems for buildings.*
- Air conditioning systems in which refrigerant piping connects a single outdoor unit to multiple individually controlled indoor units (with different capacities and power sources)
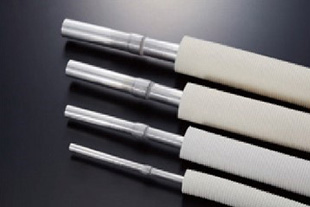
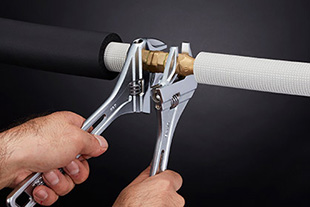
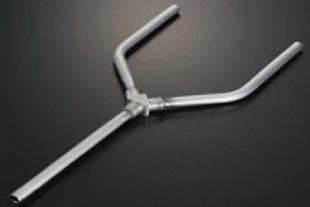
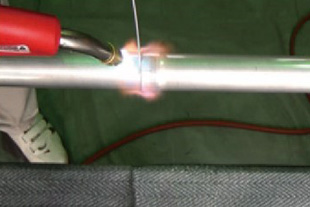
Field-tested at nine locations throughout Japan
We have conducted extensive field testing by installing aluminum piping in the air conditioning systems of administrative and temporary offices in nine locations across Japan (Akita, Yamagata, Saitama, Tokyo, Kanagawa, Hyogo, Tottori, Nagasaki, and Okinawa) with different climates and system operation patterns.
The total length of piping installed—more than 1,800 m—has been in service throughout the roughly three-year testing period with no problems.
Installed in actual buildings
As a typical example of aluminum piping in service in the real world, in October 2017, we installed an all-aluminum refrigerant piping system to coincide with the updating of the air conditioning system at the Sapporo Branch of Nihon Setsubi Kogyo Co., Ltd., one of our subsidiaries and affiliates. We also collaborated with YAMATO Inc. to install an aluminum refrigerant piping system in the air conditioning system of the new office building they constructed for AITECH CORPORATION in June 2018 and worked with our Osaka Branch to install an all-aluminum refrigerant piping system in the air conditioning system as part of the renovation of the head office building of KANKI Co., Ltd. in December of that year.
We use our experience installing these systems to accumulate insight and further advance our skills with regard to installation, and intend to promote the use of all-aluminum refrigerant pipes and the like to help save labor at our construction sites and achieve a carbon-neutral world.
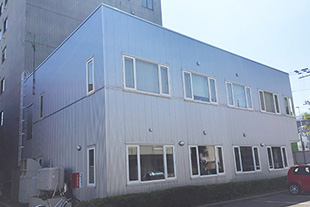
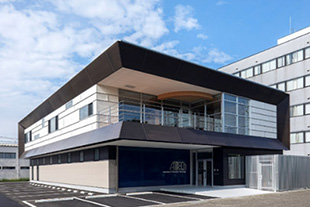
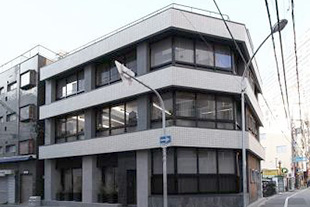
Received a Special Award
at the 36th Excellent Energy Saving Equipment Awards
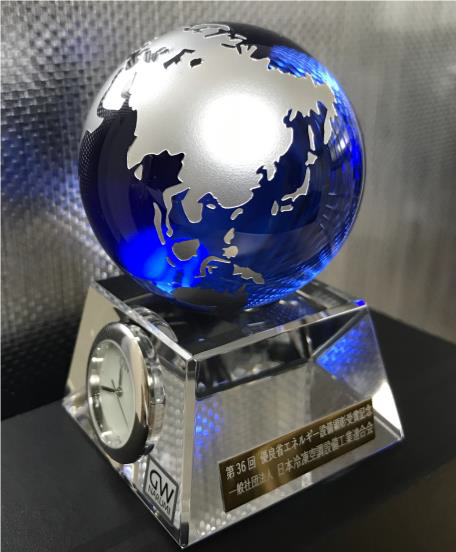
Our development of an aluminum refrigerant piping system won the Chairman’s Special Award (Photograph 8) at the 36th Excellent Energy Saving Equipment Awards hosted by the Japan Association of Refrigeration and Air-Conditioning Contractors (Minato-ku, Tokyo; Chairman: Masuo Toba).
Every year, JARAC recognizes excellent energy-saving refrigeration and air conditioning equipment with the aim of establishing and raising awareness of energy conservation. This award speaks to many things, including the major impact of switching materials and methods—a move made in anticipation of the difficulty of continuing to use copper piping due to impending societal changes—on refrigeration and air conditioning system installation work and the fact that we are developing and promoting relevant technology and spearheading industry-wide efforts.
Aluminum Plumbing Equipment Association (APEA)
committee activities and results
We are working to popularize aluminum refrigerant piping through our activities in the Aluminum Plumbing Equipment Association (APEA).
The following are examples of our efforts.
- Revised the standard for aluminum refrigerant piping (APEA 1001:2021 Coated Aluminum Alloy Piping for Refrigerant).
- Revised technical guidelines for aluminum refrigerant piping (APEA 3001:2022 Coated Aluminum Alloy Piping for Refrigerant: Installation Guidelines).
- Gave presentations on the following three topics at the APEA Technology Seminar, two of which are now available on the APEA members’ website.
“Field Testing to Compare Aluminum and Copper Refrigerant Piping”
“Important Notes on Aluminum Brazing Methods”
“Design of Piping in Aluminum Refrigerant Piping Systems (1)”
Relevant Links
- Top
- Technology & Services
- Aluminum Refrigerant Piping Systems